Main business: Multi axis robotic arms, handling robots, main robotic arms, automatic loading and unloading production lines, automatic packing and packaging lines, etc.
Business consultation hotline:
13915759590
数控车床自动化上料的实现途径
数控车床是现代制造业中不可或缺的重要设备,其加工效率和精度都得到了极大的提升。然而,传统的人工上料方式效率低下、成本高昂,并且容易出现人为误差,难以满足现代生产的需求。因此,实现数控车床的自动化上料成为提高生产效率和降低成本的重要途径。那么,数控车床怎样实现自动化上料呢?
一、自动化上料系统的构成
数控车床自动化上料系统通常由以下几部分组成:
- 上料装置:用于将原材料或半成品从料仓或传送带上搬运到数控车床的加工位置,常见的上料装置有机械手、机器人、气动抓手等。
- 输送系统:将上料装置与数控车床连接起来,并将加工后的工件传送到下一道工序,常见的输送系统有滚筒输送线、链式输送线、皮带输送线等。
- 控制系统:负责对整个自动化上料系统进行控制,包括上料装置的控制、输送系统的控制以及与数控车床的联动控制。
- 安全系统:确保整个自动化上料系统的安全运行,防止人员或设备发生意外。
二、数控车床自动化上料的实现方式
根据上料方式的不同,数控车床自动化上料可以分为以下几种:
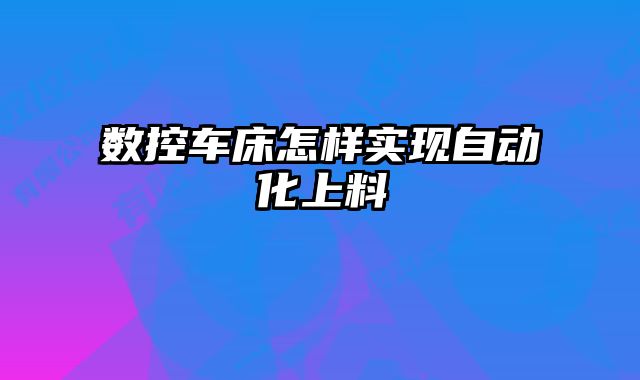
- 机械手/机器人上料:采用机械手或机器人作为上料装置,可以实现快速、精崅、灵活的上料操作,尤其适用于尺寸较大、重量较重的工件。
- 气动抓手上料:气动抓手简单易用,成本较低,适合小型、轻型工件的上料。
- 振动盘上料:适用于小型、散装工件的上料,通过振动盘将工件排列整齐,然后送入数控车床。
- 滑轨上料:适用于尺寸较小的工件,将工件放置在滑轨上,通过滑轨将工件送入数控车床。
- 自动送料机上料:适用于条料、板材等材料的自动上料,通过送料机将材料自动送入数控车床。
三、数控车床自动化上料的优势
相比人工上料,数控车床自动化上料具有以下优势:
- 提高生产效率:自动化上料可以实现连续、不间断地工作,有效提高生产效率,降低生产成本。
- 提高加工精度:自动化上料可以避免人为误差,确保工件的精度和一致性。
- 提高安全性:自动化上料可以减少人工操作,降低工伤事故的发生率。
- 提高生产效率:自动化上料可以解放劳动力,将人力投入到更高价值的岗位。
四、数控车床自动化上料的应用领域
数控车床自动化上料广泛应用于机械加工、汽车制造、航空航天、电子制造等各个领域。特别是对于批量生产、加工精度要求高、工件尺寸较大或重量较重的生产场合,自动化上料可以显著提高生产效率和降低成本。
五、数控车床自动化上料系统选型
选择合适的自动化上料系统需要根据具体情况进行考虑,主要考虑以下因素:
- 工件尺寸和重量:不同的工件尺寸和重量需要选择不同的上料装置和输送系统。
- 加工精度要求:不同的加工精度要求需要选择不同的上料方式和控制系统。
- 生产规模:不同的生产规模需要选择不同的自动化上料系统,以满足生产需求。
- 成本预算:不同的自动化上料系统价格差异较大,需要根据实际情况进行选择。
六、数控车床自动化上料的未来趋势
随着科技的发展,数控车床自动化上料系统将更加智能化、柔性化和集成化,未来将朝着以下方向发展:
- 智能化:采用人工智能技术,实现自动识别、自动规划、自动控制,提高上料系统的效率和可靠性。
- 柔性化:采用模块化设计,可以根据不同的生产需求快速调整和配置,适应各种生产场景。
- 集成化:将自动化上料系统与其他生产环节,例如仓储管理系统、物流配送系统等集成,实现整个生产流程的自动化。
七、总结
数控车床自动化上料是提高生产效率、降低成本、提升产品质量的重要手段。选择合适的自动化上料系统,并根据实际情况进行合理的设计和实施,可以有效提高数控车床的生产效率,提升企业的竞争力。
如果您需要专业的数控车床自动化上料系统解决方案,请联系江苏斯泰克智能制造有限公司。
斯泰克智能制造有限公司是一家专业从事智能制造系统研发、设计、制造、销售和服务的公司,拥有丰富的自动化上料系统开发经验,并提供包括自动码垛输送线、自动包装线、自动运输线、自动上下料、工业机器人、机械手、码垛机等恮方位的智能制造解决方案。
内容声明:本文内容由互联网收集,不代表本企业意见,本站不拥有内容中可能出现的商标、品牌所有权,不承担相关法律责任。如发现有侵权/违规的内容, 联系QQ670136485,邮箱:670136485@qq.com本站将立刻清除。