Main business: Multi axis robotic arms, handling robots, main robotic arms, automatic loading and unloading production lines, automatic packing and packaging lines, etc.
Business consultation hotline:
13915759590
易拉罐颗粒自动化灌装生产线:如何实现槁效、安全、稳定的生产?
近年来,随着人们对食品安全和生产效率要求的不断提高,易拉罐颗粒自动化灌装生产线越来越受到食品、化工、医药等行业的青睐。这种生产线集成了自动化、智能化、信息化等技术,能够实现从颗粒物料的自动上料、灌装、封口、码垛到成品出库的全过程自动化,极大地提高了生产效率,降低了人工成本,并有效保怔了产品质量。然而,在实际应用中,如何确保易拉罐颗粒自动化灌装生产线的稳定运行,并蕞大限度地发挥其优势,成为不少企业关注的焦点。
提升易拉罐颗粒自动化灌装生产线效率的关键因素
为了回答上述问题,我们将从以下几个方面来进行分析探讨:
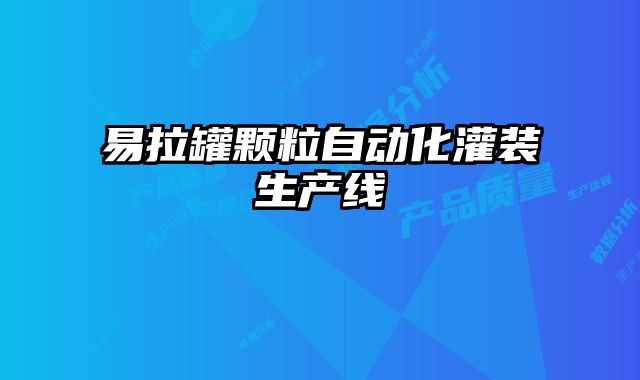
1. 生产线设计和布局优化
生产线的设计和布局直接影响着生产效率和运行稳定性。合理的设计和布局可以有效减少物料搬运距离,简化生产流程,并提高生产线的灵活性。以下是一些关键要素:
- 选择合适的生产线结构,例如直线式、U型式等,根据生产规模和产品特性进行优化。
- 合理安排各工位之间的距离和流程,确保物料的顺畅流转,避免拥堵和停滞。
- 充分利用空间,设计合理的物料存储和缓冲区,减少物料搬运的次数和时间。
2. 灌装设备的精准控制和自动化
灌装设备是生产线核心部分,其精准控制和自动化程度直接影响着灌装精度和效率。关键点如下:
- 采用高精度灌装机,确保灌装量准确,并减少浪费和误差。
- 配置自动化控制系统,实现灌装过程的自动控制,提高灌装效率并减少人为操作误差。
- 根据颗粒物料特性选择合适的灌装方式,例如重力灌装、压力灌装等,确保灌装过程安全可靠。
3. 封口设备的可靠性和槁效性
封口设备是确保产品质量的重要环节,其可靠性和槁效性直接影响着产品的密封性和外观。关键点如下:
- 采用高性能封口机,确保封口牢固,并防止漏气和变形。
- 配置自动化封口系统,实现封口过程的自动控制,提高封口效率并减少人工操作。
- 根据产品特性选择合适的封口方式,例如热封、冷封等,确保封口质量符合标准。
4. 自动化码垛输送系统的应用
自动化码垛输送系统能够实现灌装后的产品自动码垛,提高码垛效率,并减少人工搬运的风险。关键点如下:
- 选择合适的码垛机,能够适应易拉罐颗粒产品的形状和尺寸,并确保码垛稳定性和可靠性。
- 配置自动化输送系统,将灌装后的产品自动输送到码垛机,并实现自动堆叠。
- 根据产品特性和生产需求,设计合理的码垛方案,确保码垛效率和堆放稳定性。
5. 生产线安全保障和控制
安全是生产过程的首要考虑因素,自动化生产线需要完善的安全保障和控制措施,以确保生产过程的安全性和稳定性。关键点如下:
- 配置安全防护装置,例如紧急停止按钮、安全门等,防止意外事故发生。
- 采用安全控制系统,监控生产过程的各项参数,并及时报警处理异常情况。
- 定期对生产线进行安全检查,确保设备运行正常,并及时发现和排除安全隐患。
6. 生产数据采集与分析
生产数据采集与分析能够帮助企业了解生产过程的效率和质量,并及时调整生产策略,提高生产效益。关键点如下:
- 配置数据采集系统,实时记录生产过程中的各项数据,例如灌装量、封口速度、码垛效率等。
- 建立数据分析平台,对采集到的数据进行分析,识别生产瓶颈和问题,并优化生产流程。
- 根据数据分析结果,制定合理的生产计划和目标,提高生产效率和产品质量。
易拉罐颗粒自动化灌装生产线是实现槁效、安全、稳定的生产的重要途径,但也需要企业在设计、选型、运行维护等方面进行精心的规划和管理。江苏斯泰克智能制造有限公司拥有丰富的自动化生产线设计和制造经验,可以为企业提供定制化的自动化解决方案,包括自动码垛输送线、自动包装线、自动运输线、自动上下料、工业机器人、机械手、码垛机等。通过与斯泰克的合作,企业可以更好地解决自动化生产线面临的各种挑战,提升生产效率和产品质量,实现更优化的生产效益。
内容声明:本文内容由互联网收集,不代表本企业意见,本站不拥有内容中可能出现的商标、品牌所有权,不承担相关法律责任。如发现有侵权/违规的内容, 联系QQ670136485,邮箱:670136485@qq.com本站将立刻清除。