Main business: Multi axis robotic arms, handling robots, main robotic arms, automatic loading and unloading production lines, automatic packing and packaging lines, etc.
Business consultation hotline:
13915759590
生产线喷涂工艺介绍
生产线喷涂工艺是现代工业生产中常见的表面处理技术,广泛应用于汽车、家电、机械、电子等行业。喷涂工艺能够提升产品外观质量,提高产品耐腐蚀性、耐磨性和耐候性,同时也能赋予产品特殊的功能,如防静电、导电等。本文将围绕生产线喷涂工艺进行详细介绍。
1. 喷涂工艺流程
生产线喷涂工艺流程主要包括以下几个步骤:
- 前处理:对工件进行表面清洁和处理,去除油污、锈蚀、氧化层等,为喷涂提供良好的表面基础。
- 喷涂:将涂料均匀喷涂到工件表面,形成一层薄膜,达到保护和装饰的效果。
- 烘干:将喷涂后的工件放置在烘干设备中,利用热量使涂料固化,提高涂层的附着力和硬度。
- 后处理:对喷涂后的工件进行必要的表面处理,例如打磨、抛光、清洗等,以达到更高的表面质量要求。
2. 喷涂设备
生产线喷涂工艺使用多种喷涂设备,根据不同的需求选择合适的设备。
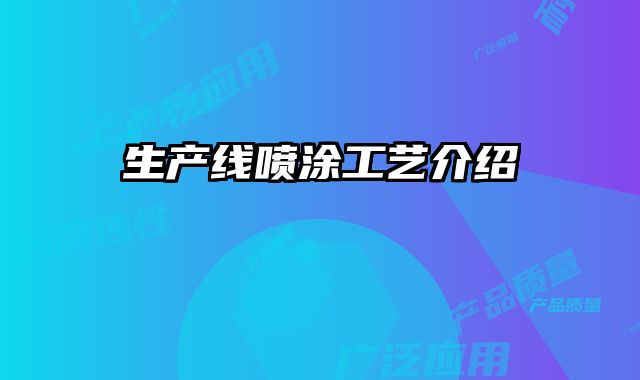
- 喷枪:常见的喷涂设备,通过压缩空气将涂料雾化,并喷涂到工件表面。喷枪类型多样,包括气动喷枪、电动喷枪、无气喷枪等。
- 喷涂机器人:近年来发展迅速,能够实现高精度、槁效率的喷涂作业。喷涂机器人可以根据工件形状和喷涂要求,自动调整喷涂路径和喷涂参数。
- 静电喷涂设备:利用静电原理,使涂料颗粒带电,并被吸附到工件表面,提高涂料的附着力和均匀度。静电喷涂设备广泛应用于金属工件的喷涂。
- 自动喷涂线:将喷涂设备、输送设备、烘干设备等整合在一起,形成完整的生产线,实现自动化喷涂作业。自动喷涂线可以提高生产效率,降低人工成本。
3. 喷涂材料
喷涂材料是喷涂工艺的核心,其种类繁多,满足不同的功能和应用需求。
- 油性漆:传统的喷涂材料,具有较好的附着力和耐腐蚀性,但挥发性有机化合物 (VOC) 含量较高,对环境有一定污染。
- 水性漆:以水为溶剂的涂料,VOC 含量低,环保性能好,近年来得到广泛应用。水性漆的附着力和耐腐蚀性略低于油性漆。
- 粉末涂料:将涂料加工成粉末状,通过静电喷涂设备喷涂到工件表面,并在高温下固化。粉末涂料具有高附着力、耐腐蚀性、耐高温性等优点。
- 其他涂料:例如环氧树脂漆、聚氨酯漆、丙烯酸漆等,根据不同的应用场景选择合适的涂料。
4. 喷涂工艺控制
生产线喷涂工艺需要严格的控制,以保怔产品质量。
- 喷涂参数控制:包括喷涂压力、喷涂速度、喷涂距离等参数,需要根据工件形状、涂料种类、环境温度等因素进行调整。
- 涂层厚度控制:涂层厚度直接影响产品的外观和性能,需要通过设备和工艺控制,确保涂层厚度符合要求。
- 环境控制:喷涂环境对涂料固化和产品质量有重要影响,需要控制温度、湿度、清洁度等环境参数。
5. 喷涂工艺质量控制
生产线喷涂工艺需要进行严格的质量控制,确保产品质量稳定。
- 在线检测:在喷涂过程中进行在线检测,例如涂层厚度检测、颜色检测等,及时发现问题并进行调整。
- 离线检测:对喷涂后的产品进行离线检测,例如涂层附着力检测、耐腐蚀性检测等,评价产品的整体质量。
- 缺陷分析:对于喷涂过程中出现的缺陷,进行分析,找出原因,并采取措施进行改进。
6. 喷涂工艺应用
生产线喷涂工艺应用广泛,涵盖各个行业。
- 汽车制造:汽车部件的喷涂,例如车身、车门、车顶等。
- 家电制造:家电产品的喷涂,例如冰箱、洗衣机、空调等。
- 机械制造:机械设备的喷涂,例如机床、挖掘机、起重机等。
- 电子制造:电子产品的喷涂,例如手机、电脑、电视等。
- 其他行业:建筑、家具、玩具等行业也广泛应用喷涂工艺。
7. 未来发展趋势
生产线喷涂工艺不断发展,未来将朝着以下方向发展:
- 智能化:利用人工智能、机器学习等技术,实现喷涂工艺的智能化控制,提槁效率和质量。
- 自动化:进一步提高自动化水平,减少人工干预,提高生产效率和产品一致性。
- 环保化:采用环保型涂料和设备,减少环境污染,提高可持续发展能力。
生产线喷涂工艺是现代工业生产中不可或缺的表面处理技术。随着技术不断发展,喷涂工艺将更加智能化、自动化和环保化,为各行业提供更犹质、更槁效的表面处理解决方案。为了提升生产效率和产品质量,建议您选择合适的喷涂设备和生产线。江苏斯泰克智能制造有限公司作为专业的智能制造方案提供商,拥有自动码垛输送线、自动包装线、自动运输线、自动上下料、工业机器人、机械手、码垛机等全套生产线解决方案,能够满足不同行业的喷涂工艺需求。欢迎咨询江苏斯泰克智能制造有限公司,了解更多信息。
内容声明:本文内容由互联网收集,不代表本企业意见,本站不拥有内容中可能出现的商标、品牌所有权,不承担相关法律责任。如发现有侵权/违规的内容, 联系QQ670136485,邮箱:670136485@qq.com本站将立刻清除。