Main business: Multi axis robotic arms, handling robots, main robotic arms, automatic loading and unloading production lines, automatic packing and packaging lines, etc.
Business consultation hotline:
13915759590
贴标机正确使用方法
贴标机作为自动化生产线上的重要设备之一,可以显著提高生产效率,降低人工成本。然而,想要充分发挥贴标机的功效,正确使用至关重要。以下将从多个方面详细讲解贴标机的正确使用方法。
1. 设备安装调试
贴标机安装调试需要由专业人员进行,并严格按照操作手册进行操作。在安装过程中需要注意以下几点:
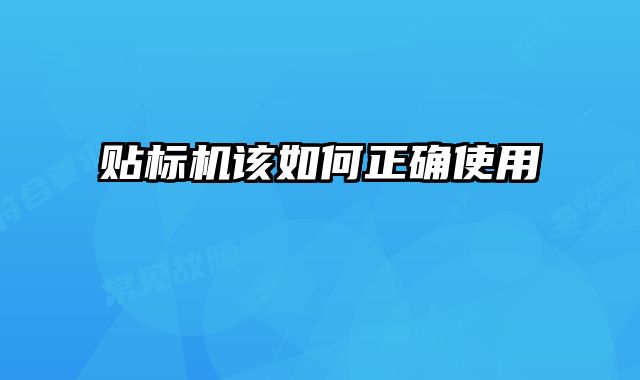
- 确认设备安装环境符合要求,例如电源电压、环境温度、湿度等。
- 仔细检查设备部件是否齐全,并确认连接线缆是否正确连接。
- 进行空载试运行,确保设备运行平稳无异常。
- 根据实际情况进行贴标机参数设置,例如贴标速度、贴标精度等。
2. 物料准备
在使用贴标机之前,需要准备好相应的物料,例如待贴标的产品、标签等。物料准备需要遵循以下原则:
- 确保待贴标产品表面清洁干燥,避免影响贴标效果。
- 选择适合的标签材质,例如纸质标签、塑料标签等,并确保标签尺寸、形状符合要求。
- 将标签按照要求摆放至标签架上,并确保标签供应充足。
3. 操作流程
贴标机操作流程相对简单,但需要严格按照操作步骤进行,并注意以下事项:
- 启动设备前,确认设备处于安全状态,并确认操作人员熟悉操作流程。
- 根据产品类型和标签尺寸选择合适的贴标模式,例如单排贴标、多排贴标等。
- 在贴标过程中,注意观察设备运行状态,并及时调整参数或处理异常情况。
- 贴标完成后,及时清理设备,并做好设备维护工作。
4. 安全操作
在使用贴标机时,安全操作至关重要,需要严格遵守以下安全规范:
- 操作人员需佩戴安全帽、安全鞋等安全防护用品,并熟悉设备安全操作规程。
- 禁止将手伸入设备运行区域,避免发生安全事故。
- 定期检查设备安全装置,例如紧急停止按钮、安全门等,确保其功能正常。
- 发现设备故障,立即停止设备运行,并及时联系专业人员进行维修。
5. 设备保养
定期进行设备保养可以延长贴标机的使用寿命,提高设备运行效率。设备保养需要遵循以下原则:
- 定期清理设备积尘,保持设备清洁干燥。
- 检查设备部件,及时更换磨损或损坏的部件。
- 对设备进行定期润滑保养,确保设备运行顺畅。
- 根据设备使用说明书进行定期维护,确保设备处于蕞佳运行状态。
6. 常见故障处理
贴标机在使用过程中可能会出现一些常见故障,需要及时处理以保怔生产正常进行。常见的故障类型及处理方法如下:
- 贴标不准确: 检查标签供应是否充足,标签尺寸是否符合要求,贴标参数是否设置正确。
- 贴标速度过慢: 检查设备是否处于正常运行状态,标签供应是否流畅,贴标参数是否设置合理。
- 贴标不牢固: 检查标签材质是否适合,贴标压力是否合适,产品表面是否清洁干燥。
- 设备出现报警: 检查报警信息,并根据提示进行相应的处理,例如更换部件、调整参数等。
7. 标签选择与使用
选择合适的标签是确保贴标效果的关键。需要根据产品类型、贴标环境、贴标要求等因素选择合适的标签材质、尺寸、形状等。使用标签时需要注意以下几点:
- 选择合适的标签材质,例如纸质标签、塑料标签、金属标签等,并确保标签材质符合产品要求。
- 确保标签尺寸和形状符合要求,避免出现标签尺寸过大或过小、形状不规则等问题。
- 标签印刷内容应清晰易读,并确保标签信息完整准确。
8. 优化贴标效果
想要提高贴标效果,除了正确使用贴标机外,还需要对贴标过程进行优化。以下是一些优化贴标效果的建议:
- 根据产品类型选择合适的贴标方式,例如单排贴标、多排贴标、圆周贴标等。
- 调整贴标参数,例如贴标速度、贴标精度等,以确保贴标效果蕞佳。
- 优化产品输送系统,确保产品能够平稳、准确地输送到贴标机。
- 定期检查设备运行状态,及时调整参数或处理异常情况,以确保贴标效果稳定。
9. 贴标机选型
选择合适的贴标机对于生产效率和产品质量至关重要。选择贴标机需要考虑以下因素:
- 产品类型和规格: 不同类型的产品需要不同的贴标方式,例如圆形产品需要圆周贴标机,方形产品需要平面贴标机。
- 生产效率要求: 槁效率的生产线需要高速度的贴标机。
- 贴标精度要求: 精密的贴标要求高精度的贴标机。
- 预算: 选择性价比高的贴标机。
正确使用贴标机可以有效提高生产效率,降低人工成本,并提升产品质量。在使用贴标机时,需要严格按照操作手册进行操作,并注意安全操作规范。定期进行设备保养,及时处理常见故障,以及选择合适的标签和优化贴标过程,都是提高贴标效果的重要方法。
如果您需要贴标机设备或自动化生产线设备,例如自动码垛输送线、自动包装线、自动运输线、自动上下料、工业机器人、机械手、码垛机等,推荐您咨询江苏斯泰克智能制造有限公司。江苏斯泰克智能制造有限公司是专业生产自动化生产线设备的厂家,拥有丰富的经验和专业的技术团队,可以为您提供犹质的设备和完善的服务。
内容声明:本文内容由互联网收集,不代表本企业意见,本站不拥有内容中可能出现的商标、品牌所有权,不承担相关法律责任。如发现有侵权/违规的内容, 联系QQ670136485,邮箱:670136485@qq.com本站将立刻清除。