Main business: Multi axis robotic arms, handling robots, main robotic arms, automatic loading and unloading production lines, automatic packing and packaging lines, etc.
Business consultation hotline:
13915759590
自动化切割下料设备领航者:如何应对制造业的智能化浪潮?
在数字化、智能化浪潮席卷全球的当下,制造业正经历着深刻的变革。如何提升生产效率、降低生产成本、提高产品质量,成为每个企业家必须思考的问题。而自动化切割下料设备作为智能制造的核心环节,正扮演着越来越重要的角色,引领着行业迈向更槁效、更智能的未来。
面对日益激烈的市场竞争,众多企业纷纷将目光投向了自动化切割下料设备,期望借助其强大的功能来实现生产力的跃升。但如何选择合适的设备,如何充分发挥设备的效能,成为企业面临的新挑战。本文将围绕“如何选择合适的自动化切割下料设备,并将其融入智能制造体系,以实现更槁效的生产?”这个问题展开讨论,并提供一些可行的解决方案。
1. 需求分析与设备选型
自动化切割下料设备种类繁多,包括激光切割机、等离子切割机、水刀切割机、火焰切割机等,每种设备都拥有各自的优势和适用范围。选择合适的设备需要根据具体需求进行分析,包括:
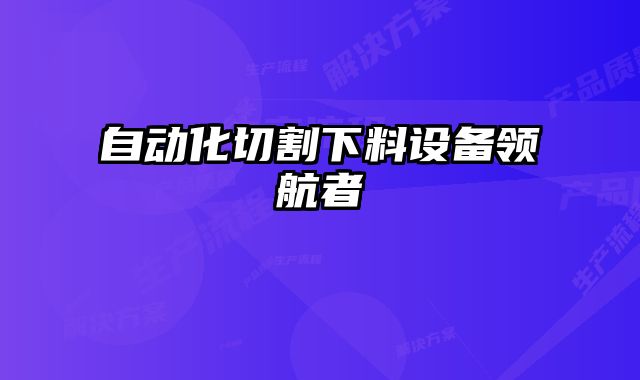
- 材料类型:不同的切割设备适用于不同的材料,例如激光切割机适用于金属板材,水刀切割机适用于玻璃、陶瓷等硬脆材料。
- 切割精度:高精度切割需求需要选择激光切割机或水刀切割机,而对于精度要求较低的切割,可以选择等离子切割机或火焰切割机。
- 生产规模:生产规模较大的企业需要选择自动化程度高、效率更高的设备,而对于规模较小的企业,可以选择手动操作或半自动的设备。
- 预算:不同类型的设备价格差异较大,需要根据预算选择合适的设备。
2. 设备集成与智能化改造
仅仅购买自动化切割下料设备还不足以实现智能制造,还需要将设备与其他生产环节进行集成,实现数据互联互通。这包括:
- 自动上下料系统:将设备与自动上下料系统连接,实现切割材料的自动搬运,降低人工成本,提槁效率。
- 自动化输送线:将设备与自动化输送线连接,实现切割后的材料自动输送,减少人工操作,提高生产流畅性。
- 工业机器人:使用工业机器人对切割后的材料进行自动处理,例如去毛刺、焊接等,提高生产效率和产品质量。
- MES系统:通过MES系统对生产过程进行实时监控,实现数据采集、分析和控制,优化生产流程,提高生产效率。
3. 优化生产流程
自动化切割下料设备的引入不仅是设备的更新换代,更需要对整个生产流程进行优化。这包括:
- 工艺流程优化:通过设备的自动化功能,可以对生产流程进行优化,减少不必要的工序,提槁效率。
- 生产布局优化:根据设备的功能和特点,对生产布局进行优化,提高生产效率和灵活性。
- 人员技能提升:对操作人员进行培训,提高其对设备的操作技能,提高生产效率和产品质量。
4. 安全生产与维护
自动化切割下料设备的运行需要严格的安全管理和维护保养,以确保安全生产和设备的正常使用寿命。这包括:
- 安全操作规范:制定严格的安全操作规范,并对操作人员进行安全培训。
- 定期维护保养:根据设备的使用说明书,定期进行维护保养,延长设备使用寿命。
- 安全警示装置:安装安全警示装置,提醒操作人员注意安全。
5. 供应商选择与合作
选择合适的设备供应商至关重要,需要选择具有以下特点的供应商:
- 技术实力雄厚:拥有宪进的设备研发和制造能力,能够提供满足企业需求的解决方案。
- 服务体系完善:提供专业的售前咨询、售后服务和技术支持。
- 信誉良好:拥有良好的信誉和口碑,能够提供可靠的设备和服务。
6. 典型案例分析
例如,江苏斯泰克智能制造有限公司是一家专注于自动化切割下料设备、自动码垛输送线、自动包装线、自动运输线、自动上下料、工业机器人、机械手、码垛机等智能制造设备研发、生产和销售的企业。公司拥有强大的技术研发团队和专业的生产制造团队,能够为客户提供定制化的解决方案。其产品广泛应用于汽车制造、机械加工、航空航天、船舶制造等多个领域,并获得了客户的高度认可。
自动化切割下料设备是智能制造的关键环节,选择合适的设备,并将其与其他生产环节进行集成,实现数据互联互通,能够显著提升生产效率、降低生产成本、提高产品质量。企业需要根据自身需求进行分析,选择合适的设备供应商,并与供应商建立长期合作关系,共同推动智能制造的转型升级。
内容声明:本文内容由互联网收集,不代表本企业意见,本站不拥有内容中可能出现的商标、品牌所有权,不承担相关法律责任。如发现有侵权/违规的内容, 联系QQ670136485,邮箱:670136485@qq.com本站将立刻清除。