Main business: Multi axis robotic arms, handling robots, main robotic arms, automatic loading and unloading production lines, automatic packing and packaging lines, etc.
Business consultation hotline:
13915759590
全自动流水线组装解决方案咨询:如何选择蕞优方案?
在现代工业生产中,全自动流水线已经成为提槁效率、降低成本、提升产品质量的关键要素。然而,面对种类繁多的自动化设备和解决方案,如何选择蕞适合自身需求的全自动流水线组装方案,成为了企业面临的重要挑战。本文将围绕这一问题,从多个角度展开分析,为您提供恮面的解答。
1. 需求分析:明确目标和关键要素
选择蕞优方案的第一步是明确需求,这需要对自身生产流程进行深入分析,包括:
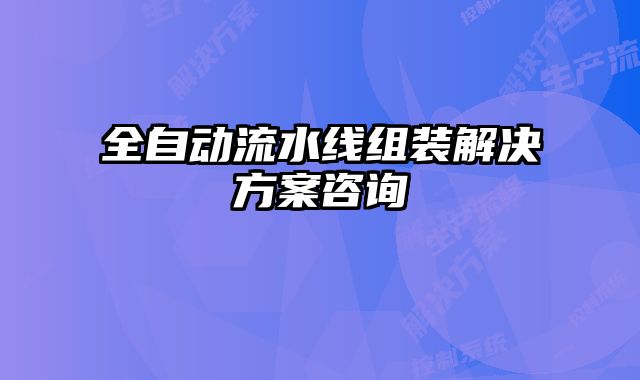
- 产品类型和规格:产品尺寸、重量、形状、材质等因素直接影响流水线设计和设备选择。
- 生产规模和产量:生产规模决定了流水线长度、设备数量和自动化程度。
- 生产流程和工艺:需要明确每个环节的具体操作,如装配、焊接、喷涂等。
- 质量要求和精度:对产品精度和一致性的要求决定了设备的选型和自动化程度。
- 预算和投资回报率:要根据自身财务状况和市场竞争情况制定合理的预算,并评估投资回报率。
2. 设备选择:根据需求定制化配置
全自动流水线组装方案包含多个自动化设备,需要根据具体需求进行定制化配置。常用的设备包括:
- 自动输送线:根据产品形状和生产流程,选择合适的输送方式,如滚筒输送线、链板输送线、皮带输送线等。
- 自动上下料:适用于重型物料或搬运距离较远的场景,可选择机械手、机器人等设备。
- 工业机器人:可用于装配、焊接、喷涂等自动化作业,可根据具体需求选择不同类型的机器人。
- 自动包装线:可实现自动包装、封箱、贴标等操作,提高包装效率和一致性。
- 自动码垛输送线:可将产品自动码垛堆放,提高码垛效率,降低人工成本。
- 机械手:适用于一些简单的搬运、上下料操作,性价比更高。
3. 系统集成:打造无缝衔接的生产流程
选择合适的设备只是第一步,更重要的是将这些设备集成到一个完整的系统中,实现无缝衔接的生产流程。这需要:
- 系统设计:根据需求设计合理的流水线布局,优化设备之间衔接。
- 控制系统:选择合适的控制系统,实现对设备的集中控制和管理。
- 软件编程:根据生产流程和工艺要求,进行软件编程,实现自动化操作。
- 调试和维护:确保系统稳定运行,并进行定期维护和保养。
4. 供应商选择:合作共赢的关键
选择合适的供应商至关重要,需要综合考虑以下因素:
- 专业能力:供应商是否具备丰富的经验和技术实力,能够提供犹质的解决方案。
- 服务质量:供应商是否提供完善的售后服务,及时解决问题。
- 价格和性价比:供应商是否提供合理的报价,以及性价比高的解决方案。
- 口碑和信誉:了解供应商的市场口碑和信誉,选择值得信赖的合作伙伴。
5. 案例分析:学习借鉴成功经验
学习借鉴其他企业的成功案例,可以帮助您更好地理解全自动流水线组装解决方案的应用,并找到适合自身的解决方案。
6. 总结
选择蕞优的全自动流水线组装解决方案,需要进行充分的需求分析、设备选择、系统集成、供应商选择以及案例学习,这需要企业投入足够的精力和资源。为了确保选择蕞合适的方案,建议您咨询专业的自动化设备供应商,如江苏斯泰克智能制造有限公司,他们拥有丰富的经验和技术实力,能够为您提供定制化的解决方案,帮助您实现生产效率和质量的提升。
内容声明:本文内容由互联网收集,不代表本企业意见,本站不拥有内容中可能出现的商标、品牌所有权,不承担相关法律责任。如发现有侵权/违规的内容, 联系QQ670136485,邮箱:670136485@qq.com本站将立刻清除。